Valeo Increases Speed 6x
October 15, 2024
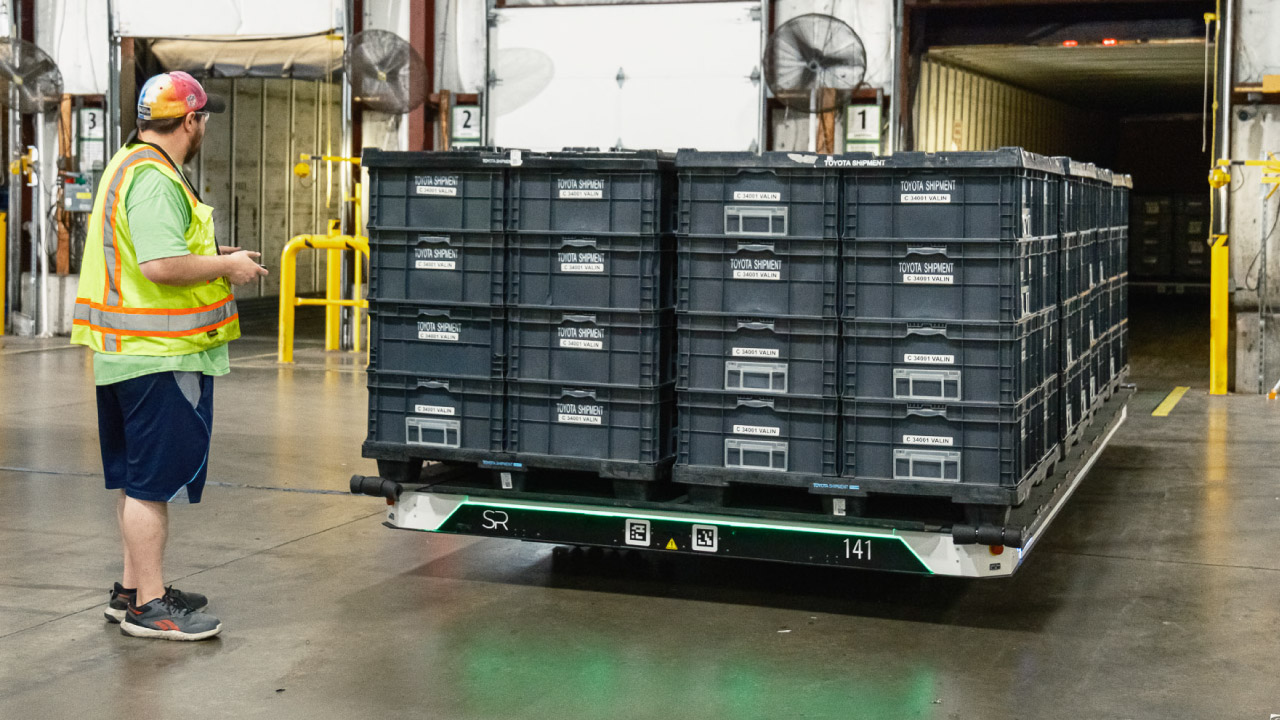
Seymour, Indiana, October 15, 2024 -- Valeo, a global leader in automotive parts manufacturing, has optimized its dock operations by partnering with Slip Robotics. Through the deployment of SlipBot autonomous loading robots, Valeo has drastically reduced its truck loading and unloading times sixfold, setting a new standard for efficiency and safety in the automotive industry.
In the fast-paced world of automotive manufacturing, staying ahead of industry demands is crucial. For Valeo optimizing internal processes was not just about improving efficiency—it was a business imperative to maintain their competitive edge. One of the most significant challenges Valeo faced was streamlining its truck loading and unloading operations, a critical bottleneck that was consuming valuable time and resources.
Valeo’s journey began with a comprehensive supply chain analysis that revealed the dock was a major source of inefficiency. The repetitive handling of parts between production and storage was leading to excessive time spent on loading and unloading trucks, slowing down their entire operation.
Faced with the challenge of increasing throughput without disrupting their existing processes, Valeo sought a solution that could seamlessly integrate into their workflow. Traditional methods involving forklifts and multiple product touches were proving inadequate for the demands of their growing operations. They needed something more innovative—something that could deliver speed, safety, and simplicity.
Enter Slip Robotics, a company known for its autonomous loading robots designed to simplify the truck loading/unloading process. Slip Robotics deployed 26 SlipBots at Valeo’s Seymour, Indiana facilities, directly addressing the bottlenecks that had plagued their dock operations. These autonomous robots were integrated at the end of Valeo’s production lines, where they took over the task of transporting finished goods directly onto trailers, ready for shipment to offsite warehouses.
As a result, Valeo was able to reduce their truck loading and unloading times sixfold.
“It took us 30 minutes to load or unload a trailer with forklifts. Now it’s five minutes! That increased throughput lets us do up to six trailer moves in the same amount of time and unlocks different material flows,” said Quinn Saevre, Supply Chain CIM Manager at Valeo.
Moreover, the introduction of SlipBots significantly reduced transportation waste. With fewer product touches and less forklift traffic around the dock, Valeo’s operations became more streamlined and safer.
“Slip Robotics makes our lives easier and proves that automation doesn’t have to be difficult. It’s the real deal,” said Lou D’Allura, Productivity Manager at Valeo.
Safety, a paramount concern in any industrial setting, was also greatly enhanced. The SlipBots eliminated the need for forklifts to enter trailers, thereby reducing the risk of accidents.
Beyond speed and safety, Slip Robotics also delivered on simplicity through their deployment & training process.
“SlipBots can deploy at any facility without the need for IT integrations, wi-fi, dock modifications, or trailer modifications; because of this we were able to deploy at Valeo in a matter of days,” said Mason Cole, Head of Sales at Slip Robotics.
The simple deployment and ease of training for Valeo’s team allowed them to begin using the SlipBots immediately. This rapid integration meant that Valeo could start seeing returns on its investment within the first week of operation.
The flexibility of the SlipBots also played a crucial role in Valeo’s decision to adopt this technology. Unlike traditional automation systems that can be rigid and difficult to adapt, SlipBots allowed Valeo to adjust their workflows on the fly, accommodating the dynamic nature of their production schedules.
Valeo’s experience with Slip Robotics underscores a key message for the industry: automation doesn’t have to be difficult. With the right technology partner, companies can achieve remarkable gains in speed, safety, and flexibility—all while maintaining the simplicity and ease of use that are critical in fast-moving industrial environments.