Loading Dock: The Best Place to Start Automating
September 20, 2024
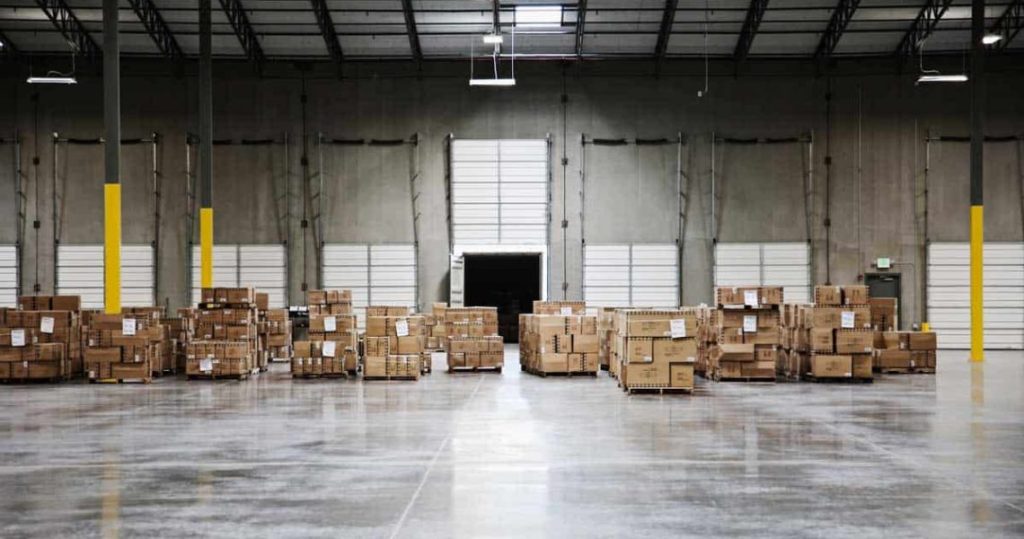
When you think of warehouse automation, what comes to mind? You might think of shuttles, vast conveyor and sortation systems, fleets of autonomous robots, or maybe even warehouse management systems.
Warehouse automation offers a myriad of opportunities to enhance efficiency, safety, and productivity. With so many options—from advanced inventory management systems to autonomous robots—deciding where to begin can be overwhelming.
The key question becomes, where can automation deliver the most immediate impact?
Why Start with Loading Dock Automation
The loading dock is the gateway of your warehouse—the critical point where everything enters and exits. Inefficiencies here create bottlenecks that ripple throughout your entire operation.
While there are many parts of the loading dock that should be addressed, one particular process stands out: trailer loading and unloading. In the past 50 years this process has largely remained the same.
Trailer loading and unloading is with a forklift is very slow and creates significant productivity bottlenecks. It can take up to an hour per trailer, leading to delays, driver idle time, and increased labor costs. These inefficiencies limit throughput and hinder the ability to meet output demands.
Not only do loading docks need a productivity boost—they need to be safer.
Over 25% of industrial accidents happen at the loading dock, and for every incident, there are hundreds of near misses. According to the U.S. Bureau of Labor Statistics, in one recent year over 38,000 work days were missed due to musculoskeletal injuries alone in the transportation and warehousing industries.
By automating the loading dock, you can have immediate impact on supply chain bottlenecks and increase safety.
Start with Autonomous Loading Robots (ALRs)
SlipBots are autonomous loading robots designed to streamline loading dock operations. These large, flat ALR are able to load and unload trailers in five minutes while carrying up to 10 pallet positions (single or double-stacked). They offer an efficient solution that requires no changes to your existing processes.
Automating the loading dock with ALRs not only enhances operational speed but also reduces the risks associated with manual handling and forklift use. Operated via intuitive hand controllers, these robots eliminate the need for operators to enter trailers and significantly reduce safety risks.
Advantages of ALRs in Loading Dock Automation
Immediate Efficiency and Safety Gains
Automating the loading dock significantly boosts speed and productivity, cutting down the time required for loading and unloading trailers. This also improves safety by reducing the need for manual labor, minimizing the risks of injuries such as slips, falls, and repetitive motion strains.
Seamless Implementation with Minimal Disruption
SlipBots are designed for easy integration, requiring no changes to your existing infrastructure or systems. This allows for a smooth transition without interrupting daily operations, enabling you to reap the benefits of automation without any downtime.
Faster Turnaround and Quick ROI
By speeding up loading and unloading, automation reduces driver wait times and improves supply chain efficiency. The resulting cost savings and productivity gains offer a fast return on investment, making it a highly effective starting point for further automation efforts.
Automate Your Loading Dock with SlipBots
Automating your loading dock with ALRs is a fast, impactful way to boost efficiency and safety. It tackles bottlenecks, reduces risk, and delivers quick results.Starting here unlocks immediate gains and long-term benefits for your entire operation.
If you’re ready to make your loading dock faster and safer, then contact Slip Robotics today.