Four Hands Increases Truck Loading / Unloading Speed
February 18, 2025
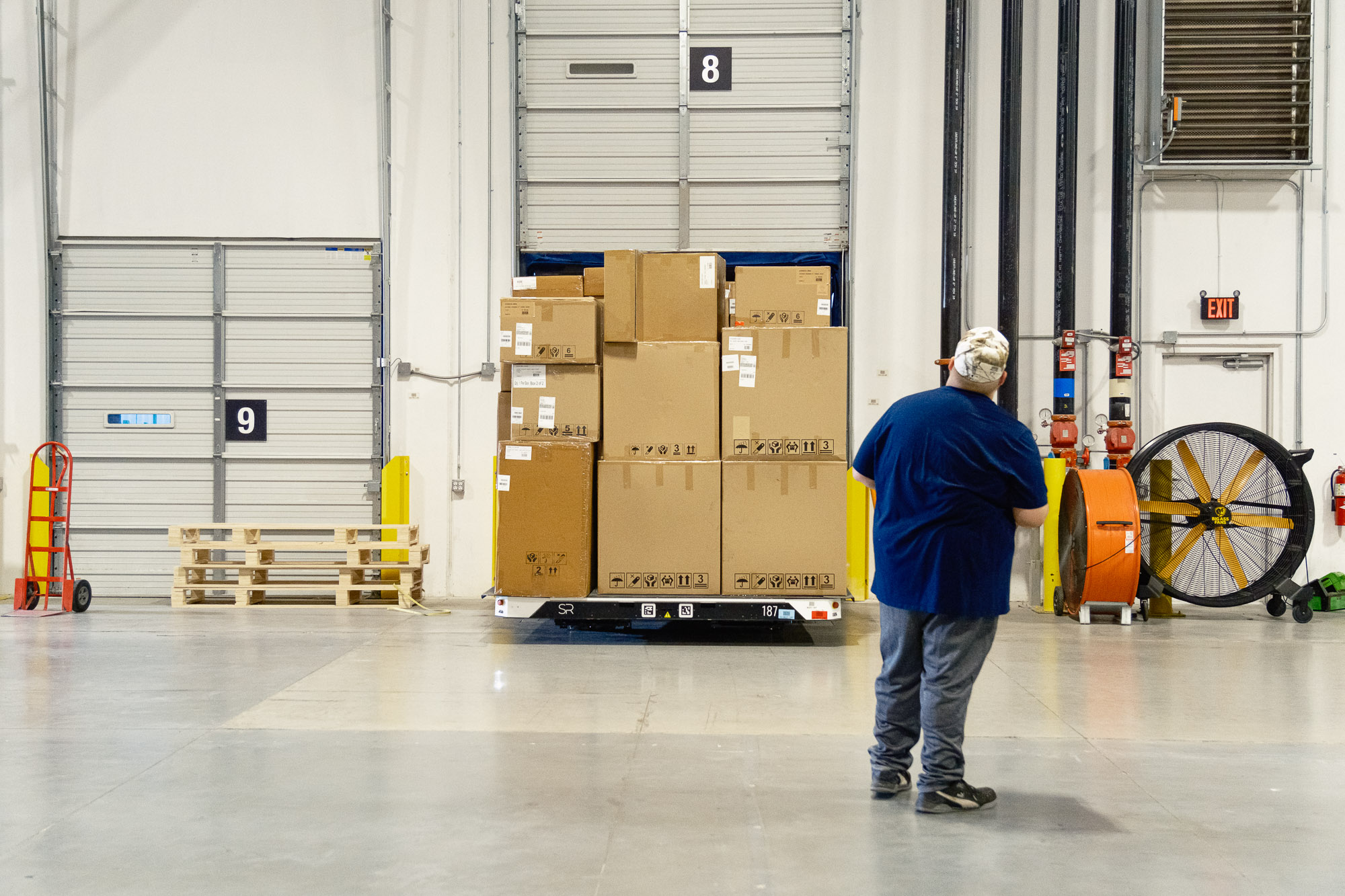
Four Hands, an international furniture designer and wholesaler, has revolutionized its operations by partnering with Slip Robotics. Deploying SlipBots across multiple facilities drove a 4x increase in throughput, 75% reduction in trailer unload time, 50% reduction in loading time, and 50% fewer product touches.
Four Hands has grown rapidly in recent years, earning them recognition on the Inc. 5000 List of Fastest Growing Companies 15 times. Scaling their operations to meet growing demand, they’ve tackled the challenges of managing a diverse product mix, ranging from 2-pound lamps to 400-pound coffee tables, across a growing network of warehouses.
Before SlipBots, loading and unloading trailers posed particular challenges, requiring 8–10 people up to 90 minutes to complete a single trailer by hand. The need for a solution was clear: automation that could handle a massive SKU mix without requiring extensive IT integrations or infrastructure changes.
“Moving heavy products across eight buildings was creating significant wear and tear on our employees and processes,” said Jim Anderson, Chief Operating Officer at Four Hands. “It’s a Tetris puzzle of being able to efficiently load and unload between those facilities, and you can’t solve all your problems by just throwing people at the situation.”
Slip Robotics addressed these challenges by deploying their SlipBot autonomous loading robots—a solution designed to simplify operations while improving both speed and safety. With no need for Wi-fi or IT integration, SlipBots were deployed rapidly and quickly adopted by the team.
“The SlipBots were operational within days, and the local tech support and training exceeded our expectations,” said Michael Leuckmeyer, Process Engineer at Four Hands. “The rapid adoption and enthusiasm from our team was remarkable, and the constant support from Slip Robotics sets them apart.
This hands-on support helped the team reimagine how they manage trailers. SlipBots have transformed the process, allowing operators to load & unload trailers from all sides rather than being limited to a single access point to the trailer. By loading the bots on the dock, the team not only loads faster but also maximizes trailer space utilization, fitting more product into each trailer.
“We’ve reduced unloading time by almost 75%, loading times by 50%, and product touches by 50%,” said Billy Malady, VP of Operations at Four Hands. “It’s also cut our nighttime contract labor by half while maintaining the same throughput, if not more. It had very quick payback.”
The 50% reduction in product touches has also delivered significant safety improvements. The decrease in manual handling has minimized the physical strain on employees, cutting the risk of injuries associated with heavy lifting and repetitive tasks. Additionally, employees now stay safely on the dock, avoiding the hazardous conditions of trailer heat and the risks of pull-away incidents.
“It really does what it’s advertised to do. Being able to implement solutions that help the human provides a practical and realistic solution that delivers value,” said Anderson.
Looking ahead, Four Hands plans to further leverage Slip Robotics to support its expanding operations. With plans for additional warehouse facilities and an unwavering commitment to innovation, the company is well-positioned to remain a leader in the furniture industry.
“We’re very comfortable that as we continue to grow, this will be a permanent part of our solution,” said Malady.